Christine Wagner
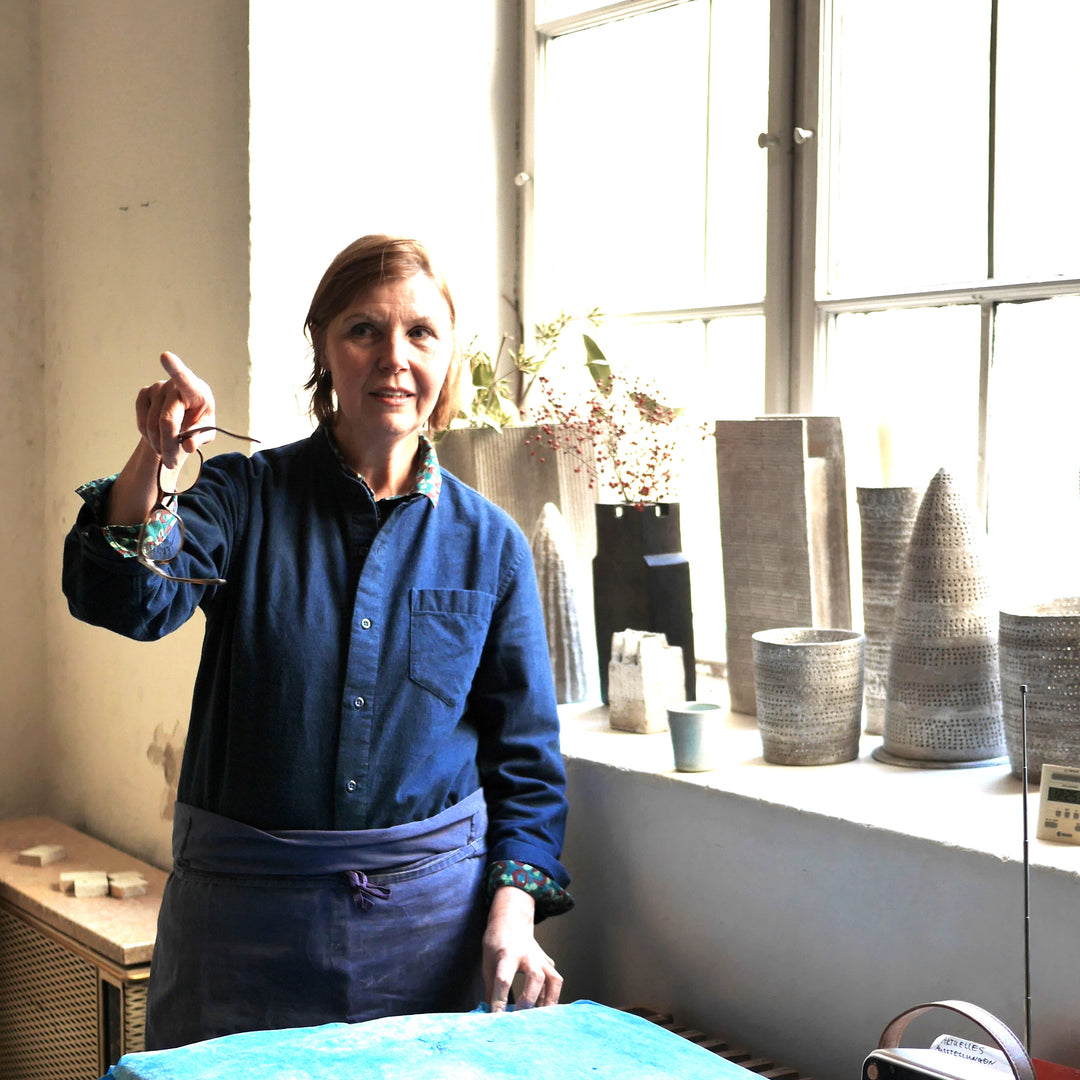
Cookies
We use cookies. Many are necessary to operate the website and its functions, others are for statistical or marketing purposes. With the decision "Accept only essential cookies" we will respect your privacy and not set cookies that are not necessary for the operation of the site.
Essential
Statistics & Marketing
Accept all
Only accept essential cookies
Individual cookie settings
Save & close
Essential
Essential cookies enable basic functions and are necessary for the proper functioning of the website.
Statistics & Marketing
Marketing cookies are used by third-party vendors or publishers to display personalized advertising. They do this by tracking visitors across websites.
About the object: Christine Wagner's stoneware pedestal vase with two openings is 22.5 cm high, approx. 18 cm long and 7.5 cm wide. The ground plan of the vase gives it its unusual shape. The grooved plates are covered with white engobes made of chalk and kaolin and seem to breathe. Reduced to the essentials, Christine Wagner's unique stoneware pieces impress with their pure beauty.
Production process: The surfaces of Christine Wagner's hand-built stoneware vases have grooved, linear or stamped structures and follow linear patterns. Made from self-mixed, coarse-grained clay from the Westerwald, the grainy structure or stamped pattern is emphasized by applying white engobes of chalk and kaolin to the dry surfaces. This creates a multi-layered surface effect. The thin application of kaolin with a brush creates a glaze-like effect, like a whitewashed clay wall. Firing in a gas kiln with a reducing flame is essential for the appearance of the vases and objects. By removing the oxygen in the reduction firing at 1280 degrees, Christine achieves a color spectrum of the fired clay from light grey to beige or darker brown tones, depending on the clay mixture.
We offer reliable shipping for our products to various destinations. Here are our shipping options:
Germany:
EU countries:
You can find a list of the countries to which we ship here.
Please note that the stated delivery times are estimates and may vary depending on the destination and current circumstances. We are always trying to get your orders to you as quickly as possible.
For further information or special inquiries about shipping, please do not hesitate to contact us. We are at your disposal!
Christine Wagner (*1959 in Munich) completed her ceramic apprenticeship from 1980 - 1983 with Yasoji Sasaki in Toki-shi, Japan. This was followed by study trips to Korea and China and the continuation of her ceramic apprenticeship until 1985 in Landshut, Germany. Christine Wagner received her ceramics diploma from the University of Art in Linz, Austria in 1989.
She has been running her workshop studio in Munich since 1990 and since 2010 Christine has been teaching at the technical college for design in Karlsfeld and Unterschleißheim near Munich (since 2014).
Christine Wagner's excellent works are regularly shown in exhibitions and can be found in private and public collections (Die Neue Sammlung, Pinakothek der Moderne, Munich; Museum für Kunst und Gewerbe, Hamburg; Bavarian State Chancellery, Munich; Peter Siemssen Foundation, Wesenberg / Ratzbek).
Christine about her work: "The focus is on the exploration of simple geometric shapes: the ground plan defines the form. By structuring the surfaces, there is a multitude of possibilities to vary the shape of the vessels. Minimal interventions allow the composition of the forms to be reassembled again and again.
Clay as a material, surface treatment and firing with an open flame have been my field of research for many years. The self-mixed, coarse-grained clay made of red and grayish clay from the Westerwald, the surface design with kaolin, the use of various white engobes and the use of metal oxides for the dark surfaces result in the specific appearance of my ceramics.
All the elements work together. This unique quality drives me to continue working with clay as a material, because it enables the combination of shaping and the change in materiality through the melting process in the kiln."